In this article, we outline how to choose a linear guide for your application and environment.
By Lindsey Brimage and Eric Schultz | Thomson Industries
Ian Miller | Motion Industries Canada
Designers of linear motion systems often find themselves weighing the pros and cons of round versus profile (also known as square) linear guides. Many considerations come into play while trying to determine which technology to implement; this is only further compounded when environmental extremes are a concern. Too often, the choice of linear guide technology is made late in the design process and based on assumptions. Taking time to perform a nuanced review can make the difference between a simple design and a complex one, affecting performance, assembly time and total cost.
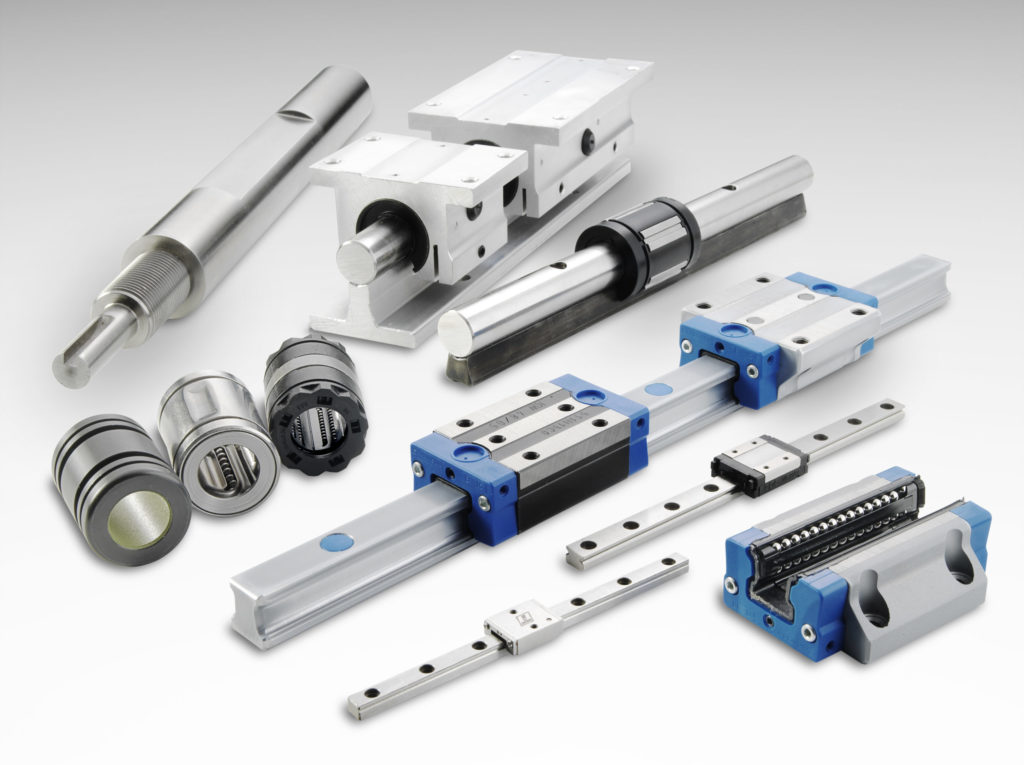
Round and profile rails are often interchangeable functionally, but there are marked differences even within those categories. Making the right choice for your application can spur significant advantages in cost, performance and durability. This article discusses how those differences play out in applications complicated by environmental extremes. Issues of fluid or solid particulate egress, temperature extremes, corrosion, shock and vibration design considerations will all be discussed.
Before going through these complicating factors, it is important to remember the pros and cons of both round and profile linear guides in an undemanding environment. Understanding these technologies and how they can be best applied to an application is always the first step in good design practice.
Round rails for forgiving installations
Round rail is the older of the two technologies and has been around for about 80 years. Typically, the most economical option (relative to component cost) round rails have a lower load capacity and looser accuracy. The design of the round rail is very forgiving; this forgiveness can be either a strength or a weakness depending on your application. For applications where loose tolerances are acceptable or where low component costs are more critical than tight tolerances, round rails are an excellent option.
Round rails are self-aligning and very forgiving of issues that arise from poor parallelism or variation in rail height for systems using more than one rail. This technology provides a smooth and low drag platform. The eloquently simplistic profile boosts highly effective sealing and a natural contamination resilience. In addition, round rails don’t need the time and expense of mounting surface machining and are the only option for end-supported applications.
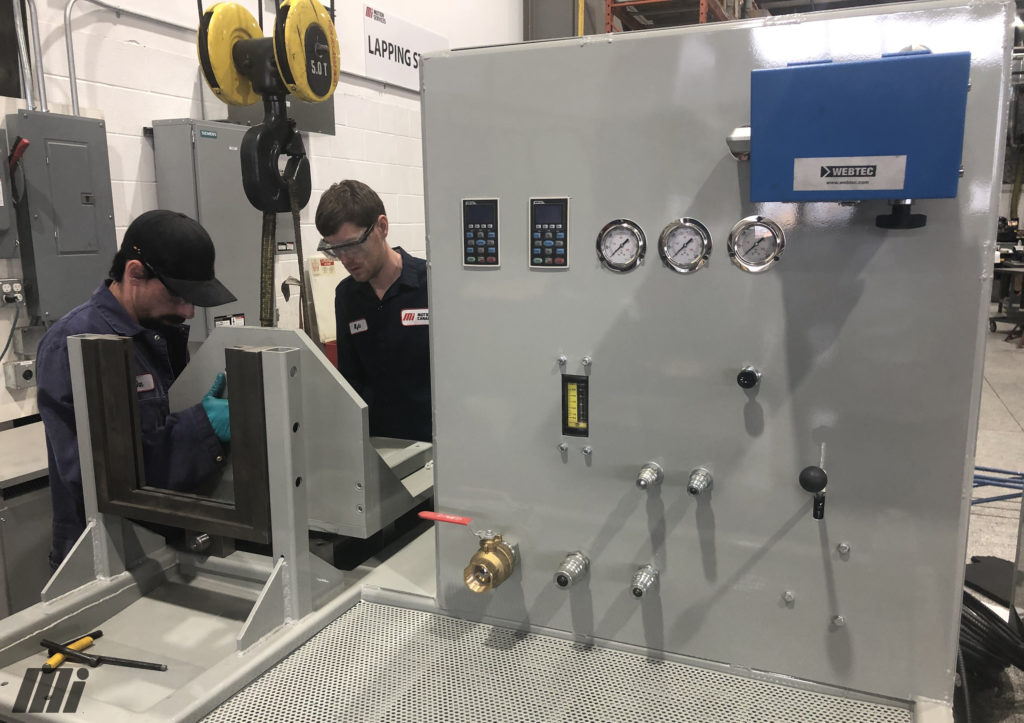
Profile rail (also known as square rails) for tighter accuracy
Profile rail is the newer of the two technologies and has been around for about 40 years. Typically the more expensive of the two options, profiled rail has a higher load capacity and much tighter accuracy. The design of the profile rail isn’t forgiving, and this strictness can be of either great benefit to or a complicating factor for your design. The nature of this technology lends itself well to applications where extremely tight levels of precision are required, or where excessive loading is inherent to the task at hand. The compact nature of the system can help to reduce the overall size of the equipment, but higher preloads could increase in drag.
Further, the nature of the profile rail mounting and installation process (including surface machining) makes it very unforgiving of poor parallelism or variation in rail height for systems that use more than one rail. Manufacturing systems using profile rails need higher precision. Their elaborate, albeit compact, profile also suffers from more complex sealing and comparably poorer contamination resilience.
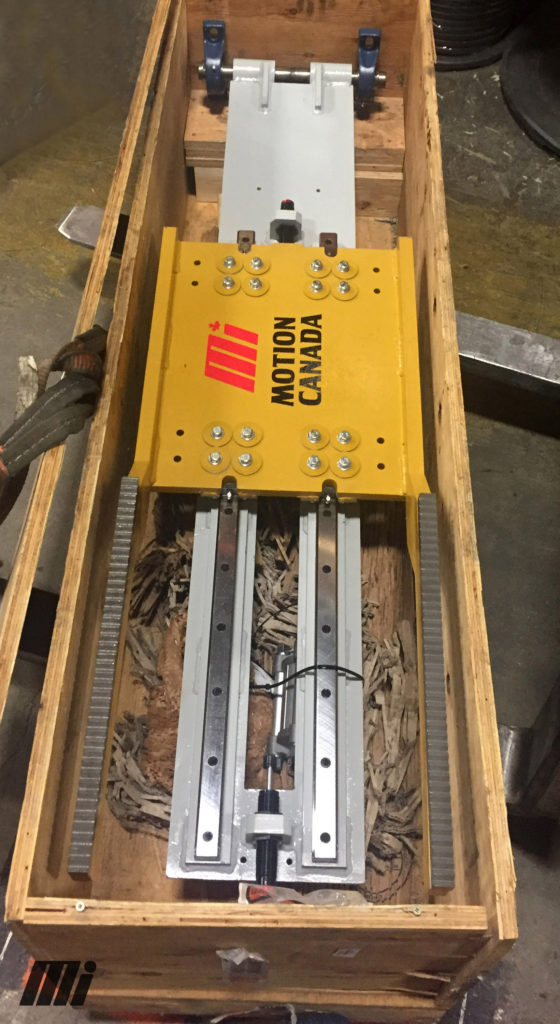
Fluid-exposure considerations when specifying linear rail
Exposure to fluids such as water, fog and high humidity can lead to corrosion of either rail type. Under pressure, as in washdown situations, fluids can wash lubrication away. Exposure to corrosive fluids such as chemical sprays, fuel oils, acidic food products, hydrocarbons, urea and fertilizers can introduce safety threats as well as contribute to wear, downtime and performance degradation. Both round and profile guides will differ in their fluid handling abilities based on sealing, lubrication type, material selection, coatings, mounting and standards compliance, which is particularly important in the medical and food industries.
For both round and profile guides, full-contact seals and proper lubrication will prevent rust from developing on the raceways of steel components. Seals on round guides tend to cause less drag due to their simple circular geometry, but low-drag options are available for profile rail assemblies. Profile rail carriages may also employ longitudinal seals that protect against ingress from the bottom of the assembly.
材料的选择是另一个关键组件fluid handling ability of a system. Round rails have an advantage in that they can use non-hardened stainless-steel shafting. This makes them attractive for clean environments such as those found in the semiconductor and medical industries as well as the harsh environments of food processing. Higher loads may need hardened shafting. This can be accomplished with advanced coatings, which can extend component life 200-fold.
Coating options are comparable for both round and profile rails and in both cases, increased corrosion protection may involve tradeoffs with hardness. For example, Armaloy chromium coating provides moderate corrosion resistance and hardness of 78 HRc. In contrast, austenitic stainless steel such as 300 series is more corrosion resistant but more expensive — and has HRc hardness levels only in the 20s. Austenitic stainless steels are typically only recommended for use with plain-style bushings. Martensitic stainless steel, such as 440C, also offers improved corrosion resistance over carbon steel but can reach hardness levels in the 50s — and thus can be used with certain proprietary ball-bearing linear bushings.
In fact, other factors may come into play when considering coating options. Stainless steel, for example, is an especially good choice for food-grade environments or other applications in which users might be concerned about flaking off of the plating.
Well-chosen machine geometry, orientation, and guarding can also improve its ability to handle excessive fluid. Orienting the guide in a way that will minimize fluid penetration into bearing surfaces or that will promote runoff will also improve fluid handling. Profile rails are more compact, so they can provide more flexibility if standard mounting geometries are possible. The quality of the mounting surface finish is key to having the most flexibility during profile rail installations. To more facilitate installation flexibility, profile rails come in different mounting configurations. They can, for example, bolt from top or bottom and offer multiple methods to cover and protect bolt holes from debris, including cover strips, plastic rail plugs and metal rail plugs.
When more flexibility is required, round shafts have the advantage. They can be configured in many ways to facilitate holding the ends of the shaft and can even provide structural support in a larger assembly. Options to implement reduced diameters, flats or to drill through the case of the shaft, on center or radially, add to mounting flexibility. The self-aligning design of round rails is also more forgiving of poor parallelism and variations in rail height.
Safeguarding linear guides against solid particulate
Solid particulates such as metal, wood chips, extremely fine glass, ceramic dust or flour get into moving parts and impact wear and performance. Particulates can fall onto round or profile rails or may be airborne. Guide manufacturers address dust and particulate handling through sealing and wiper designs that protect against solid contaminants that land onto bearing surfaces.
Getting a robust seal on a profile rail is challenging because wipers must conform to the ball tracks which are ground in the rail and may increase drag — in fact, twice as much drag as with round linear bearings. Low-drag wiper designs for profile rail carriages help to minimize this problem but don’t eliminate it.
Profile rails might use scrapers to remove heavier particulate or bellows to shield raceways from any dust or particulate accumulation. Round rails have natural debris-shedding capabilities due to the curvature of their shafts. Although profile rail tracks are hidden from direct access, they don’t necessarily shed debris.
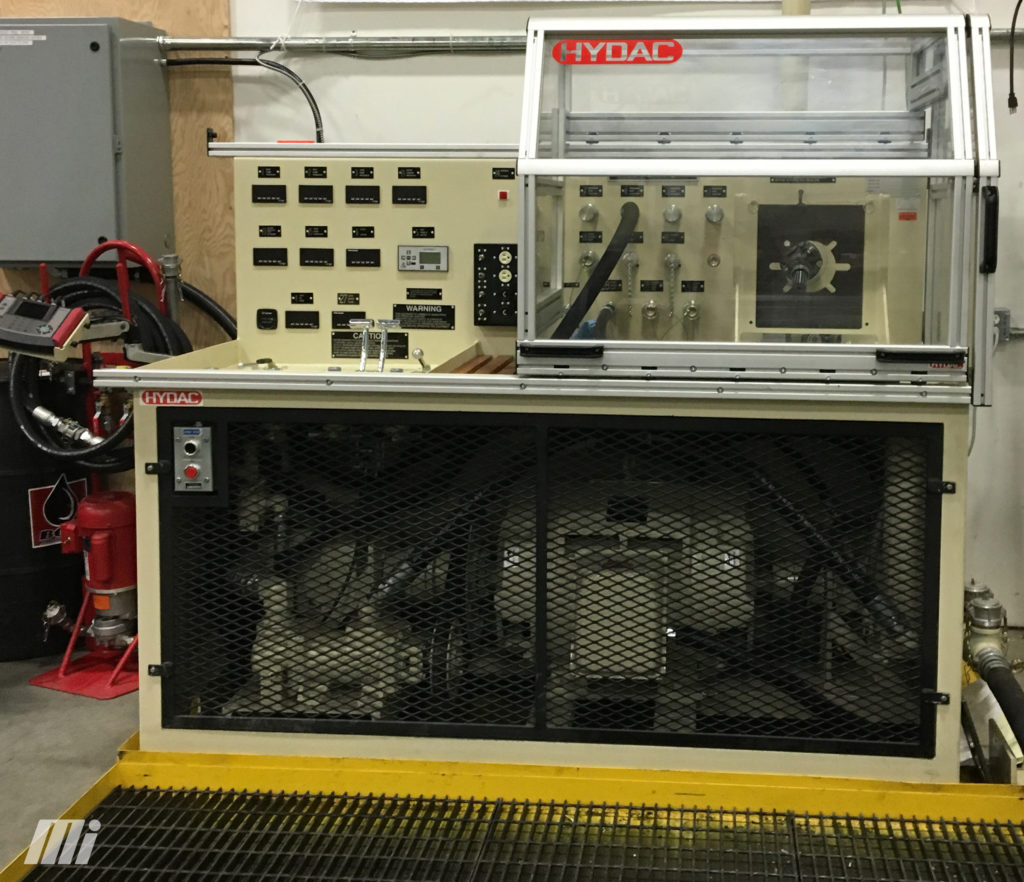
How round and profile rail handle extreme temperatures
Extreme temperatures tend to have the greatest effect on plastic components, such as seals and recirculation mechanisms. Temperatures above or below the lubrication’s rating can cause components such as base oil, thickener and additives to separate and reduce. Fluctuations in temperatures can cause condensation, which leads to corrosion as well as thermal expansion and contraction in steel and aluminum.
Round rails can accommodate all-steel or stainless steel bearings with no plastic components. Both steel and stainless steel provide a wider operating temperature profile, but the stainless steel bearings have less load capacity than steel. Also, the plastic end caps and recirculation tubes in profile rail often prevent them from being used in extreme temperatures.
Vibration and shock resistance
Constant torque and movement can weaken a component over time and cause failure. Shock loading, as with an instantaneous impact load, affects all bearings. The heavier the load, the greater the problem, and because profile rails can handle heavier loads, shock is more of an impact force. In all cases, however, the rail is scaled to the capacity of the normal load and not to the shock load. The greatest impact is with heavy machinery, where the shock is more detrimental just because of the pure mass involved.
Profile rails are also more tolerant of heavy impacts because they offer various preload options, which can make them more resistant to other impacts that don’t affect the rolling element.
Round rails are less tolerant of impact due to their natural clearance fit. They do however outperform profile guides when a fluid driving force is applied to the rail because they are less likely to pull up on race areas than are profile rails.
Round or profile rail — the final verdict
The decision on whether to use round or profile rail depends on the application. As always, begin by establishing the motion profile and the essential performance characteristics. Then evaluate the options according to their advantages or disadvantages for each environment.
Profile and round rails can both be used in wet, corrosive, dusty and high shock and vibration environments, as long as the considerations are made for their design differences, accessories and overall precision and load requirements.
Where precision beyond the capability of round rails is essential in hazardous environments, coatings may be specified — or the designer will need to factor in the operational limits and incremental costs of the profile rails.
Profile rails may have some advantages in wet environments because their compact size provides more flexibility in mounting to avoid moisture, but if forgiving tolerances, nonstandard geometries or end-supported configurations are required, round rails have the clear advantage. There are many useful online tools available that help users weigh the tradeoffs among various hazardous conditions.
For more information, visitMotion IndustriesatMotionIndustries.com/designworld. Also watch this video on mounting options for round shafting …
About the authors
Lindsey Brimage is Product Line Specialist — Linear Bearings and Guides at Thomson Industries.
Lindsey supports the linear bearings and guides business while directing sales and customer support with technical product inquiries and training. She earned her Bachelor of Science in Chemical Engineering at the University of Pittsburgh and has worked at Thomson for two years.
Eric Schultz is Key Account Manager at Thomson Industries.
Eric develops and maintains strategic long-term relationships with key clients to collaborate on mutually beneficial projects, create solutions to meet objectives and support existing business. He earned his Bachelor of Science in General Engineering at the University of Illinois at Urbana-Champaign and has worked at Thomson for two years.
Based out of Calgary, Ian Miller, P. Eng. is National Services Business Development Manager of Motion Industries Canada.
He has more than a decade of hydraulic and electrical experience in the field including system design, troubleshooting, onsite installations, as well as technical training and support.
You may also like:
Filed Under:Linear Motion Tips,Linear motion • slides