由史蒂文帕斯特纳克,C.O.工程师 - Slevoil轴承
由Mike Santora编辑
通过产生完全支撑旋转轴的加压油膜,流体动力轴承操作。在正常操作期间没有轴 - 轴承触点,当油膜打破时,在启动和关闭时,次要磨损主要发生。流体动力学轴承通常用于主要关注的应用中保护大型且昂贵的轴;恰当的轴承材料选择至关重要。本文将巴比特/白色金属和基于PTFE的聚合物的性质与流体动力学轴承应用中的轴承材料进行了比较。虽然研究继续在新材料上,但该行业发现巴比特目前在今天提供的材料中无与伦比。
流体动力学轴承是一种特殊类型的流体润滑的滑动轴承,通过产生完全分离轴和轴承在正常操作期间的流体膜的流体润滑轴承。从根本上,流体动力学轴承只有三个部分:旋转轴,轴承本身和流体润滑剂,通常是油。在数百种不同的应用中发现了流体动力学轴承,并且以长寿命,高负荷承载能力和出色的阻尼能力而闻名。
在理想的条件下,流体动力学轴承可以由能够承受该系统施加的温度和压力的任何材料制成。在正常操作期间,轴和轴承通过油膜完全分开。这意味着理论上,只要存在油膜,轴和轴承就不会磨损。然而,这些轴承通常由于污染,轴未对准和转子不平衡而在非理想条件下运行。此外,这些系统可以定期停止并重新启动风扇,电机或其他机器。油膜厚度是表面速度的函数,因此在启动和关闭期间发生大多数轴承磨损。然而,油膜也可以分解并导致轴磨损的其他原因。
大轴和修理或更换它们所需的停机时间非常昂贵,因此轴承需要能够在较小的污染和轴未对准的情况下操作,而不会导致轴损坏。重要的是要注意,轴和转子可以非常重,具有大的旋转动量,这意味着它们可能需要很长一段时间来完成完整的停止。
水动力轴承的基础
选择合适的轴承材料,了解流体动力学轴承的基本操作非常重要。为了使流体膜的空间开发,设计了流体动力学轴承,使得轴和轴承之间存在径向间隙。根据申请,间隙量可以变化。当。。。的时候
轴没有转动,它坐在轴承中,由极薄的油层分开。当系统开始时,
油分子的润滑性是轴和轴承之间的唯一润滑。这意味着轴和轴承表面中的粗糙度,小“峰和谷”,直接接触。这被称为“边界润滑”,并且是摩擦最大的地方,以及大部分轴承和轴磨损发生的地方。

图。1
随着轴速度的增加,在两个表面和膜之间强制出来的油开发完全分开两种表面。这被称为“全膜润滑”或“流体动力润滑”。图1示出了(a)边界润滑,其中粗糙度与(b)流体动力润滑,其中两个表面完全被油膜分离。
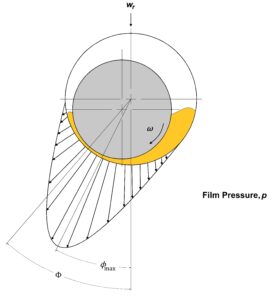
图2
图2显示了正常操作期间的流体动力轴承的压力分布。在流体动力润滑期间,轴不完全沿着负载方向静置,由W表示R.。相反,由流体剪切力产生的压力产生的会聚油楔子,使得轴略微达到侧面,如图所示。因此,流体动力学轴承可以被认为是自我压力的。称为φ的负载方向和最小膜厚度之间的角度称为“姿态角度”。流体压力也不均匀。它在最大压力角度最高,表示为。最小膜厚度和可以计算。随着轴承的操作,即使轻微的转子不平衡也使轴在薄膜上轨道或“反弹”,从而产生膜压的周期性变化。
轴承材料选择标准
在轴承和润滑:机械设计师的工作簿,士绅识别轴承材料的以下9个特性,以确定流体动力学轴承应用中的适用性[2]。
嵌入性是轴承材料嵌入小污染物并防止它们损坏轴的能力。当污染物与可嵌入的轴承材料接触时,流体压力迫使它们进入材料中,如图3所示。

图3.
同时,流体中的剪切力使轴承材料“冷流动”并覆盖污染物。可嵌入的材料可以嵌入少量污染物而不会受到损害。这不仅在正常操作期间保护轴,而且在边界润滑期间保护轴。
适当性
一致性是材料在未对准或制造缺陷的情况下“磨损”的能力[2]。当轴和轴承之间存在未对准时,轴承的末端将有边缘装载,如图4所示。

图4.
适形轴承将在边缘迅速磨损,允许更均匀地分布压力,而不适合的轴承将更有可能在这些位置变得更容易失效并损坏轴。
热膨胀系数
热膨胀是指响应于温度的增加而增加材料的尺寸。随着轴承温度从环境温度升高到稳态工作温度,轴承应以类似于轴的速率径向扩展,以防止间隙的过度变化,这会影响轴承性能和振动。在流体动力轴承应用中,轴通常由钢合金和研磨成其最终尺寸制成。因此,考虑的轴承材料的热膨胀系数应与钢的热膨胀系数相当。
导热系数
导热率是指材料转移热量的能力。轴承材料应散发流体剪切和摩擦产生的热量。具有高导热率的材料将使热量通过轴承材料散热,而导热性低的材料将充当绝缘体,允许热量积聚。这降低了最小膜厚度,并可能导致轴承磨损。

图5.
抗压强度
该材料不应过度地在由轴和流体膜压力引起的载荷下变形。流体动力学轴承特性部分由径向间隙决定,过度变形会影响轴承性能。通常,非常高的强度材料没有流体动力学轴承中所需的嵌入性和形容性特性。通常通过将轴承材料的薄层用由支撑轴承表面的更强大的材料制成的衬里来衬里薄层来实现平衡,如图5所示。
疲劳强度
由于循环载荷,材料不应失效。在大轴承中,疲劳不限于启动和关机。由于转子不平衡,它也可能由轴的轨道或“弹跳”导致轴的“弹跳”。
磨损率
轴承材料不应过度磨损,特别是在边界润滑期间。但是,它应该比轴材料更柔软。与抗压强度一样,耐磨性过多的轴承材料可能不是理想的。如果润滑失效或过度振动,轴承应保护轴免受损坏。
兼容性
材料兼容性是指轴承和轴组合的电阻,以抓取,刻痕或粘在边界润滑期间的微焊缝。在钢轴的情况下,唯一会造成相容性风险的唯一轴承材料是黑色金属。
耐腐蚀性能
有一些应用在可以暴露于可以腐蚀轴承材料的污染物,影响其嵌入性,适当性和磨损率的污染物。严重的污染可能会影响润滑剂的性能,并且应避免,无论轴承材料如何。然而,合适的流体动力学轴承材料应至少具有轻度水平的耐腐蚀性。
巴巴特/白色金属轴承
Babbitt,也称为白色金属,是指通过Sir Isaac Babbitt在1839年首先发明的一组锡或铅基合金.Babbitt合金是由于它们成功满足的能力超过100年的标准流体动力学轴承材料。以上适当轴承材料选择的特性。
在大多数流体动力学轴承上,Babbitt直接在薄层中浇铸到由铸铁,钢,青铜或其他硬质金属制成的轴承衬里,产生金属键。尽管巴比特具有比铸铁或钢的抗压强度较低,但衬里材料提供足够的结构支撑。Babbitt还具有高导热率,使其能够将热量从轴承表面从轴承表面转移到衬里。BABBITT合金的热膨胀系数与碳钢的热膨胀系数非常相似,确保轴和轴承之间的间隙保持一致的冷热条件。Babbitt合金是柔软的,提供非常高的嵌入性和符合性。
在图6所示的轴承上,轴的研磨不一致,导致轴上的聊天。由于其高度的符合性,轴承“磨损”在轴上的高点,分布轴载荷并防止轴磨损。如果发生润滑的损失,Babbitt轴承将由于温度和“擦拭”而增加,暂时连接到轴并在机器停止时保护其免受损坏。
Babbitt作为轴承材料的缺点是与制造轴承相关的成本。Babbitt是一种相对便宜的材料,但将其铸造到衬垫上的过程可以是劳动密集型的。巴巴特还具有相对较低的上温限制,至少与其他材料相比。虽然其熔点超过500°F,但其正常操作的温度限制小于250°F。然而,大多数工业润滑剂的性能限制正常工作温度至约200°F。
基于PTFE的轴承
近年来,在使用聚合物的利益增加了作为流体动力学轴承中金属材料的替代品。有数百种不同的聚合物用于轴承应用,包括尼龙,聚甲醛(POM,也称为“缩醛”),聚醚醚酮(PEEK)和聚四氟乙烯(PTFE)的变体。这些材料中的每一种适用于各种应用,并且具有不同程度的负载承载能力,表面速度容量,抗苛性化学品,可接受的温度范围和兼容材料。在大轴承中,PTFE和基于PTFE的聚合物似乎具有作为流体动力学轴承的应用的最佳性状组合,并且在推力轴承应用中流行。
PTFE在流体动力学轴承应用中最期望的性质是它具有非常高的最大工作温度。许多基于PTFE的聚合物被宣传为能够承受超过400°F的温度,尽管今天的极少可用的油可以在这种情况下运行。同样重要的是要注意,在200°F的温度下运行呈现安全危险。当与钢配对时,PTFE也具有非常低的摩擦系数,减少了所需的启动扭矩[3]。然而,一旦达到流体动力润滑,摩擦系数很小,因为没有轴承接触。
PTFE在流体动力学轴承中的另一个好处是制造成本明显低于巴比特。不需要在高温下铸造,PTFE可以直接粘合到衬里。虽然受试者上的可用技术文献有限,但是诸如具有高嵌入性的多种基于PTFE的聚合物也具有高嵌入性。
基于PTFE的材料的缺点包括它们的导热性和热膨胀系数。PTFE具有低导热率,使其充当绝缘体并防止热量从轴承表面流入衬里。尽管PTFE具有高的最大工作温度,但油温的相对较小的增加将降低油粘度和薄膜厚度,并且大幅增加会急剧降低轴承寿命。如果PTFE层足够厚,则高热膨胀系数会导致轴之间的间隙和轴承过度变化,这会影响轴承性能,甚至可以造成快速失效。
最近,在流体动力学轴承施加中测试了一种基于PTFE的聚合物。轴被研磨,并在具有油循环系统的受控环境中进行测试。轴承经受恒定负荷,未对准。
最初,材料似乎非常有前途。然而,在大约1,000小时后,轴承材料未能严重得分,如图7所示。油也非常变色,在推力套环和油环上留下黑色残留物。在安装时非常光滑的聚合物的表面光洁度在两个衬里一半都非常粗糙,如图8所示。似乎PTFE的聚合物没有适当地嵌入导致加速磨损的污染物材料和轴损坏。
基于几十年的行业经验和可用数据,Babbitt此时是流体动力轴承最合适的轴承材料。它的挪用能力和适当性水平与行业遇到的任何材料都不匹配。基于PTFE的聚合物的测试将继续,但现有的测试数据对其作为流体动力学轴承材料的适用性提高了严重问题。
与测试环境不同,许多轴承应用经历了更高程度的转子不平衡,周期性负荷和未对准,有些则没有滤油系统,并且在脏污环境中具有更高水平的污染。修理或更换轴,以及所需的停机时间总是比更换轴承更昂贵。该行业发现,由于其轴节省益处和验证的工业应用成功历史,因此制造巴巴特轴承的额外成本值得为费用。
Baldor Dodge.
Baldor.com.
提交:轴承
告诉我们你的想法!